Maximizing Efficiency: Optimizing Your Aluminium Door Window Manufacturing Process
In today's competitive market, efficiency plays a crucial role in the success of any manufacturing operation, including the Aluminium Door Window Manufacturing process. As companies strive to reduce costs and increase output, optimizing every aspect of their production line becomes paramount. This blog explores key strategies to enhance productivity and efficiency within aluminium window and door manufacturing, focusing on the integration and utilization of advanced technologies such as the Aluminium Door Window Manufacturing Machine.
By adopting innovative techniques and modern machinery, manufacturers can streamline their workflows, minimize waste, and improve product quality. From initial design to final assembly, each stage of production presents opportunities for optimization. In this blog, we will delve into various methodologies and best practices that can transform aluminium door and window manufacturing, ensuring that manufacturers not only survive but thrive in an ever-evolving industry landscape. Join us as we uncover the secrets to maximizing efficiency and productivity in this vital sector.
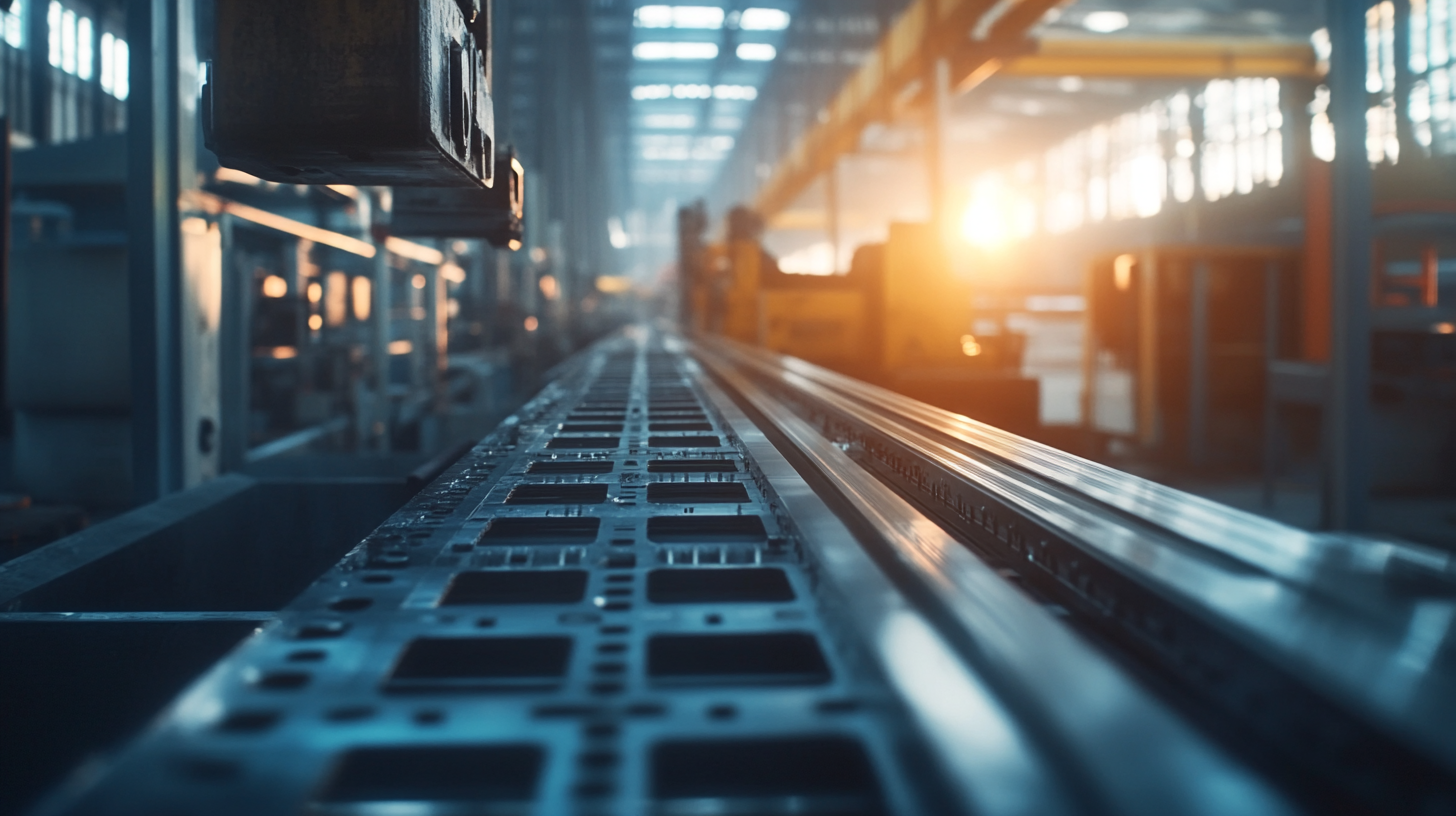
Identifying Key Areas for Improvement in Aluminium Door Window Production
Optimizing the aluminium door window manufacturing process begins with identifying key areas for improvement. One critical aspect is the supply chain management. Companies should evaluate their material sourcing to ensure they are obtaining high-quality aluminium at competitive prices. Streamlining supplier relationships can reduce lead times and minimize costs. Implementing just-in-time inventory systems can also help maintain optimal stock levels while reducing waste.
Another significant area for improvement is the manufacturing workflow. Conducting a thorough analysis of the production line can uncover bottlenecks that slow down the process. Techniques such as value stream mapping can be employed to visualize and enhance the flow of materials and information. Automation of repetitive tasks can also boost productivity, allowing skilled workers to focus on more complex and value-added activities.
Quality control is essential in the aluminium door window production process. Establishing strict quality assurance protocols at each stage of manufacturing can prevent defects and ensure product reliability. Investing in advanced inspection technologies can help identify flaws early, reducing rework and material waste, thus improving overall efficiency. By focusing on these key areas, manufacturers can significantly enhance their operations, leading to higher quality products and greater customer satisfaction.
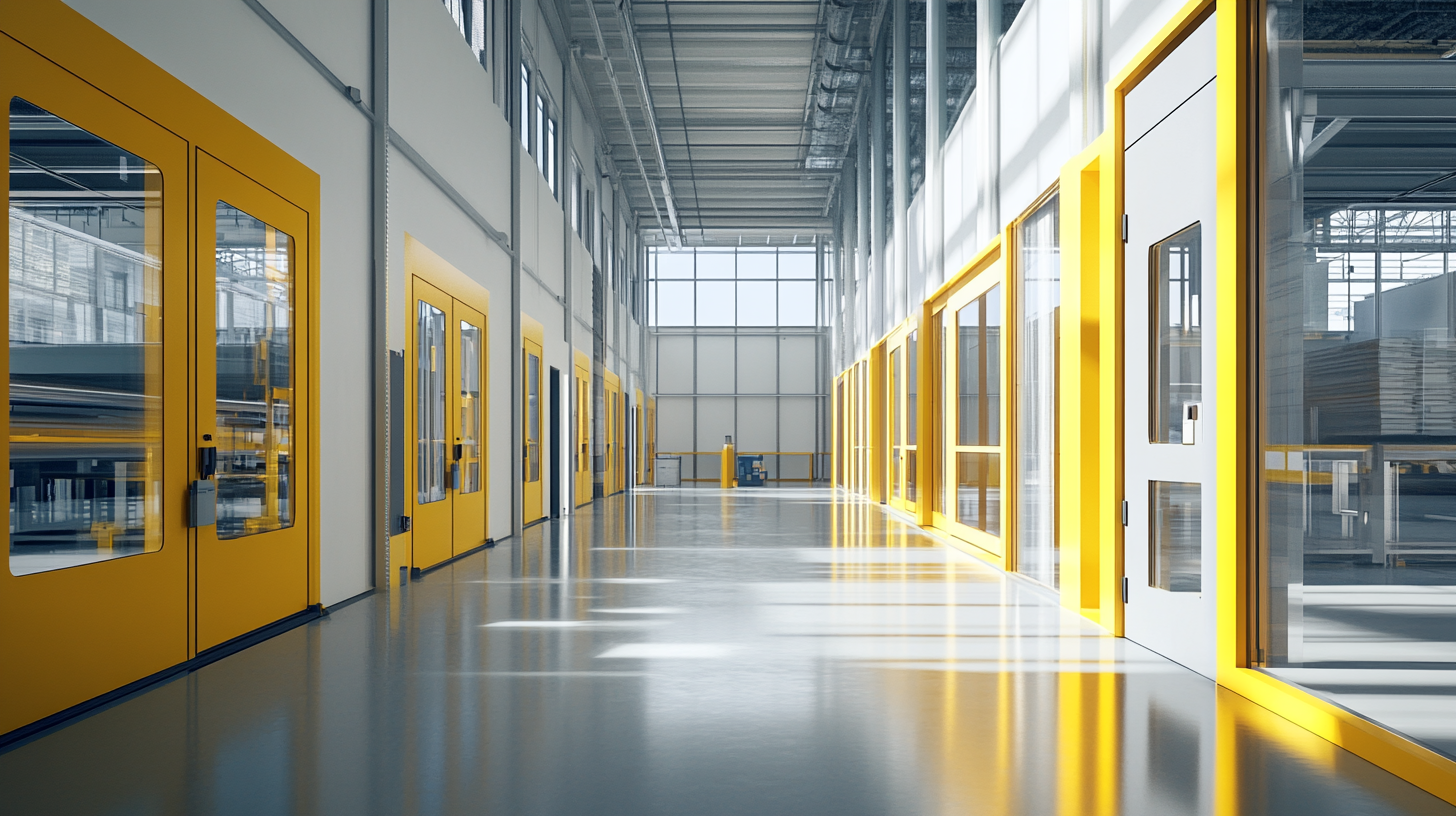
Streamlining Supply Chain Management for Enhanced Efficiency
In the competitive landscape of aluminium door and window manufacturing, streamlined supply chain management emerges as a crucial factor in enhancing operational efficiency. By focusing on optimizing the supply chain, manufacturers can significantly reduce lead times and minimize costs. One effective strategy is to establish strong relationships with key suppliers. By fostering open communication and collaboration, companies can ensure timely delivery of materials and components, thus preventing delays in production.
Another critical aspect is the adoption of advanced technology and automation tools in supply chain processes. Implementing systems for real-time inventory tracking and demand forecasting enables manufacturers to respond swiftly to changes in market demand. This not only helps in maintaining optimal stock levels but also reduces the risk of overproduction or stockouts, further enhancing efficiency in the manufacturing workflow.
Additionally, integrating a robust logistics strategy can streamline the movement of goods from suppliers to the factory floor. By utilizing data analytics, manufacturers can identify the most efficient transportation routes and methods, subsequently cutting down on transit times and costs. This integrated approach not only supports timely deliveries but also contributes to a more sustainable manufacturing process by reducing waste and emissions.
Maximizing Efficiency: Aluminium Door Window Manufacturing Process
Implementing Advanced Manufacturing Technologies in Your Process
In the ever-evolving landscape of aluminium door and window manufacturing, implementing advanced manufacturing technologies is crucial for enhancing efficiency and staying competitive. Automation is at the forefront of this transformation, allowing manufacturers to streamline their operations. For instance, robotics can automate repetitive tasks such as cutting, welding, and assembling components, significantly reducing the possibility of human error and increasing production speed. This not only ensures consistent quality but also frees up skilled labor for more complex tasks, allowing for greater innovation within the workforce.
Another critical technology is the integration of smart manufacturing systems, which utilize the Internet of Things (IoT) to monitor and optimize production processes in real time. By collecting data from machines and production lines, manufacturers can identify bottlenecks, predict maintenance needs, and adjust workflows seamlessly. This data-driven approach leads to more informed decision-making and efficient resource allocation, ultimately resulting in reduced waste and lower operational costs.
Moreover, employing advanced simulation and design software can enhance product development cycles. These tools enable manufacturers to visualize and test designs virtually before physical production, shortening the time needed to bring new products to market. By using advanced materials and engineering techniques, companies can also create more energy-efficient and durable aluminium products, appealing to environmentally conscious consumers. Embracing these technologies not only boosts productivity but also positions manufacturers as leaders in innovation in the aluminium sector.
Training Employees: The Role of Skill Development in Productivity
In the competitive world of aluminium door and window manufacturing, employee training plays a pivotal role in enhancing productivity and ensuring efficiency throughout the production process. By investing in skill development, companies can cultivate a workforce that is not only adept at handling complex machinery and technology but also understands the intricacies of their specific roles within the manufacturing ecosystem.
Regular training sessions can empower employees with the latest techniques and best practices, which can significantly reduce errors and waste on the production floor. For example, employees trained in the nuances of aluminium fabrication are more likely to optimize material usage, minimizing costs and maximizing output. Furthermore, fostering a culture of continuous improvement encourages workers to seek innovative solutions, directly contributing to overall productivity.
Moreover, a well-structured training program enhances employee morale and job satisfaction. When workers feel valued and see opportunities for personal and professional growth, they are more likely to remain engaged and committed to their tasks. This not only leads to higher quality products but also increases retention rates, saving companies the time and resources involved in recruiting and training new hires. In this way, skill development directly correlates with a more efficient and productive manufacturing process.
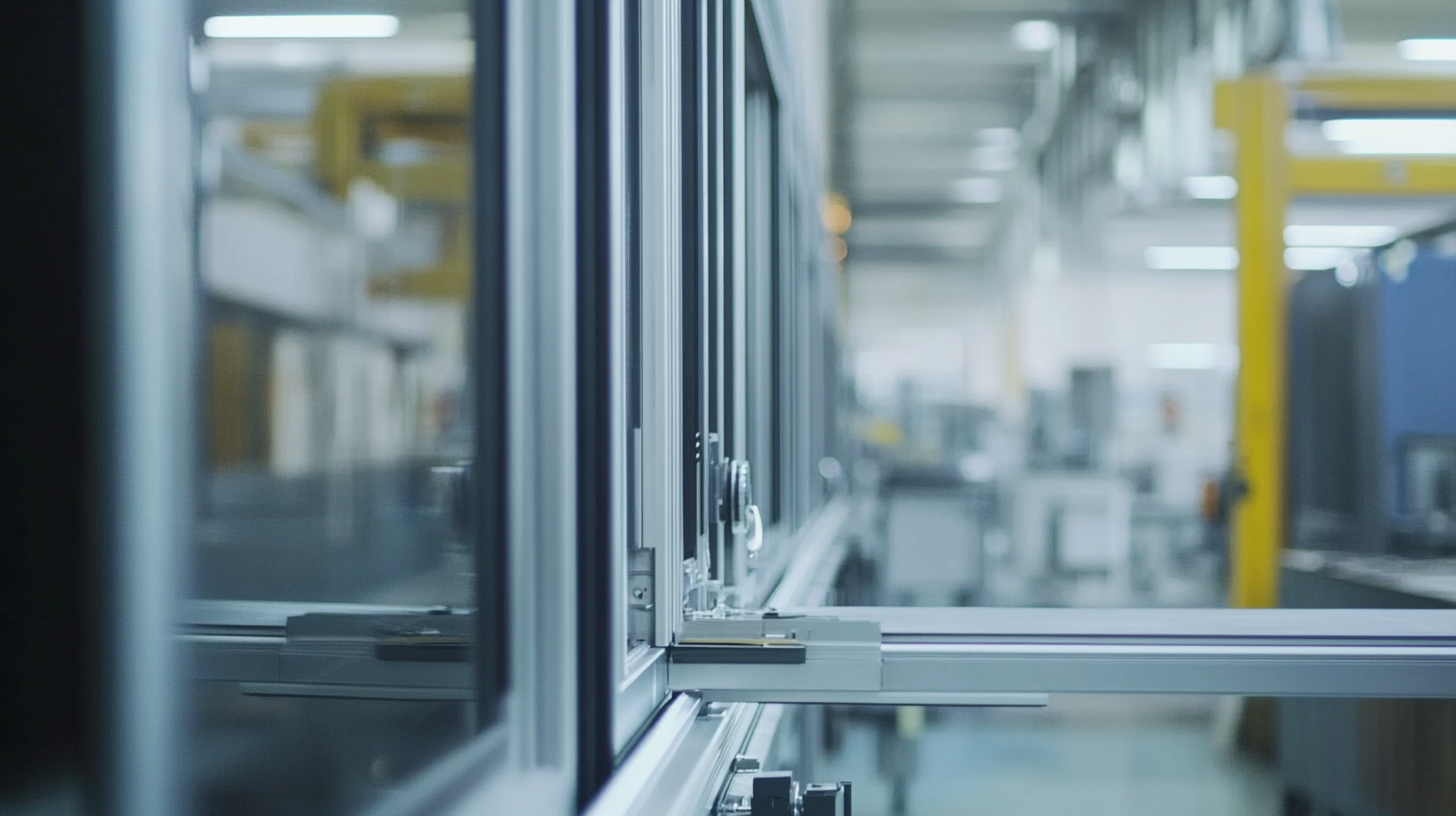
Measuring Success: Key Performance Indicators for Aluminium Manufacturing
In the competitive landscape of aluminium door and window manufacturing, optimizing processes is crucial for maximizing efficiency. A key component of this optimization involves establishing comprehensive Key Performance Indicators (KPIs) that guide manufacturers in measuring their energy consumption and productivity. According to recent studies, the incorporation of an energy management control system has shown to significantly enhance efficiency by leveraging waste heat recovery and establishing a clear energy baseline consumed per unit volume.
The energy baseline identified through these management systems allows manufacturers to tailor their processes, ensuring that energy usage aligns with best practices within the industry. For instance, by using data retrieved from lifecycle assessments, companies can pinpoint phases in production that consume excessive energy and seek innovative alternatives, potentially reducing energy use by up to 20% as reported in recent industry surveys. Furthermore, market trends indicate a growing demand for sustainability, making it imperative for manufacturers to not only adopt these efficiency metrics but also actively report on them to stakeholders.
Performance indicators such as energy consumption per unit of production and percentage reduction in waste can help the aluminium industry track its progress towards sustainability goals. A notable finding revealed that aluminium part industries implementing waste energy recovery strategies have been able to achieve an increase in operational efficiency by 15% while simultaneously lowering overall production costs. These advancements underscore the importance of measuring success through effective KPIs, enabling manufacturers to remain competitive while aligning with global sustainability efforts.